Eli Lilly Pharmaceuticals
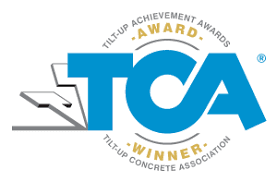
Stats.
81,000 SF of casting bed, used up to 3 times
22,500+ CY of concrete
1,050+ Tons of rebar
267,520 SF of tilt panels
289,600 SF of Slab on Grade (258,000 SF of which was Ductilcrete)
368,280 SF of Slab on Metal deck (198,020 Sf of which was 5’ over 3’ warehouse grade high capacity)
Synopsis
Spline, Building 2, to Administration, Building 1 Transition, Stacked Panels:
The Administration Building finished floor was set to match the second-floor elevation of the Spline Building. A height change of 21’ was required. The transition had to occur within the first 65’of the building to allow for grade-level access of the lower-level floors. The lower level of the spline had to be designed to retain exterior grade soil needed for the transition. The panels required a depth of 14”to retain the soil. At the second-floor level, the panel stopped, and a second insulated panel was stacked on top to provide consistency in appearance with the remaining project panels. The top panel was 10” thick, 4”-2”-4” structural composite insulated panels, using the IconX system. The area for crane access was extremely tight, leaving only 35’ of crane road to walk the crane, with the steep uphill incline on one side and the outside face of Building 4 on the other side. At the farthest point, the critical pick in this was 99%.
A secondary hydro crane was used to fly in all the braces for attachment to helical ground anchors on the exterior of the building footprint. A total of 10 sets of two panels were stacked on top of each other in this area.
Spline, Building 2 Corridor, Panel Bracing Challenges:
Building 2 was a corridor that ran the length of the job (750’) connecting 9 other buildings together. While only 20’ wide, this corridor was the resting place for panels with a height of 54’—which created quite an issue concerning casting space.
As a result, nearly 81,000 SF of casting bed was placed and used to cast on multiple times. In total, over 75% of all panels were cast on temporary beds with a total of 267,520 SF in panels. Some 280 LF of Building 2 bordered Building 3, which, per the plan, had a 22’ depressed basement from finished grade.
At the time, this basement was nothing but a pit with a cast-in-place wall surrounding it. So, the panels placed on the border of Building 3 had to be set on top of this cast-in-place wall with a 22-FT drop below, allowing no place to brace to. As a result, the panels on the opposite side of the corridor were braced to the ground with Super 42’s, and the 17 panels set of the Cast in Place wall were braced back to those panels. This was made more complex because the bracing had to be properly positioned so that steel could be erected in this corridor.
Braces were ultimately positioned vertically on the wall between the roof joists and the structural connections for the pipe support system. Secondarily, the basement wall was also 10” thick, the same as the tilt wall panels to be placed on top; this required specialized connections.
Building 3:
Building 3 contained a basement level, which took much longer than anticipated to construct, and the grading of the site was an issue. To get back on track, the GC posed the idea of erecting tilt panels after the steel and 2nd floor slab on metal deck had been fully completed. As a result, all 62 panels on Building 3 were cast with 16-point double-clutch picks as well as 8-point top pick inserts. We performed a two-rigging, transition pick for all the panels in this building. Since the 2nd floor slab on metal deck (5” over 3” deck) had been placed previously, we braced to the 2nd floor deck with 22’ braces and MB slam anchors. By utilizing the structural deck on the 2nd floor, the team was able to eliminate the time and costs associated with exterior anchoring. These panels were insulated composite panels with top pick inserts in the 4” thick wythes.
Building 2 spandrel Panel:
At the end of the Spline Building, the end panel required an opening of 15’x33’ across a 22’ wide section. The panel was broken up into three pieces as a previously built elevator shaft was blocking erection of the full panel. Panel 252 consisted of two 33’legs and a 20’3”x20’ spandrel panel across the top.
Pipe Support Framing:
The spline also contained a third level of framing to support large amounts of piping. The piping was coordinated late in the project, which posed challenges as the piping was designed to feed from the spline into the adjoining buildings. Holes were coordinated and placed in the panels to allow for the piping to pass through as needed. The piping contained steam, which created some challenges with thermal forces through the 750’ spline. The introduction of steam, which would occur in the piping at the time the system was charged for operation, would require special load consideration on the support steel and connections to the panels.
Project Challenges
The project is a complex of buildings that were interconnected with a common “spline.” The spline of Building 2 was 22’ x 750’, with Buildings 3, 4, 5, 6, 7, and 10 attached to the spline from both the north and south. An Administration Building (Building 1) ties into the east end of the spline. The project is a multi-level production facility with floor-level changes and passthroughs between buildings. Some sections of the building had to retain soil, and some areas contained cast-in-place basement walls, as well as double walls and other design elements to meet FM global standards.
Adding to the complexity of the project, the design/build contractor was working with the owner to accommodate changes in the building systems during the construction process. Building additions were made during construction to increase the overall footprint. Accommodations for a future ASRS system was accounted for with knockout panels.